Table of Contents
ToggleWhat is Slab Casting?
Slab casting is a process used in the manufacturing of concrete slabs, which are used as a structural component in buildings and other construction projects. The process involves pouring concrete into a mold or formwork, allowing it to harden, and then removing the formwork to reveal the finished slab.
Main Components for RCC Slab Casting
Concrete is a mixture of cement, water, aggregates, and other additives. The aggregates used in concrete can be natural or artificial, and typically include sand, gravel, crushed stone, or recycled materials such as crushed concrete or recycled glass. The type and amount of each material used in the concrete mix will depend on the desired strength, workability, and other characteristics of the finished concrete.
Reinforcement steel, also known as rebar, is used to provide additional strength and support to the concrete slab. Reinforcement steel bars are placed in the formwork before the concrete is poured, and they are secured in place using ties or other fasteners. The rebar provides additional tensile strength to the concrete slab, which helps to resist cracking and other forms of damage.
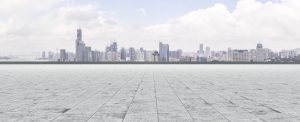
Other materials used in slab casting may include formwork, which is typically made of wood, steel, or other materials and is used to provide a mold for the concrete during pouring and curing. Release agents are also used to prevent the concrete from sticking to the formwork during the casting process. Additionally, sealants and coatings may be applied to the finished slab to provide protection against moisture, weathering, and other forms of damage.
Overall, the main materials used in slab casting for houses are concrete and reinforcement steel, which are combined to create a strong, durable, and long-lasting structural component. Careful attention must be paid to the selection and quality of these materials, as well as to the construction process itself, in order to ensure that the finished slab meets the required specifications and standards for safety and performance.
Slab Casting Process
The slab casting process typically starts with the preparation of the formwork. The formwork is usually made of steel, wood, or other materials and is designed to the desired dimensions and shape of the slab. The formwork is then coated with a release agent to prevent the concrete from sticking to the formwork when it is poured.
Next, the concrete is mixed and poured into the formwork. The concrete must be carefully placed to ensure it is evenly distributed and that there are no voids or air pockets. The concrete is then vibrated to remove any trapped air and to ensure that the concrete is compacted uniformly.
After the concrete is poured, it is left to harden and cure for a specific period. The curing time varies depending on factors such as the type of concrete used, the temperature and humidity of the surrounding environment, and the size and thickness of the slab.
Once the concrete has cured, the formwork is removed, and the slab is finished. The finished slab is inspected for defects such as cracks, surface imperfections, or other issues that may affect its strength and durability.
Slab casting is a common process used in the construction industry to manufacture concrete slabs that are used as a structural component in buildings and other construction projects. The process requires careful planning, preparation, and execution to ensure that the finished slab meets the required specifications and standards.
- Proper reinforcement placement: Make sure that the steel reinforcement is placed properly and secured in place, as it is essential for the strength of the slab.
- Ensure formwork is stable: The formwork or the moulds for the slab should be stable and strong enough to hold the weight of the concrete until it sets.
- Check for voids or cavities: Use vibrators during the casting process. Check the formwork for any voids or cavities that can lead to uneven or weak spots in the slab.
- Avoid overloading: Avoid placing too much weight on the slab, especially during the initial setting period, as it can cause cracks or damage.
- Curing: Proper curing of the slab is essential to prevent cracking or shrinkage. Make sure that the slab is kept moist for at least 7-10 days to achieve proper curing.
- Temperature and weather: Casting the slab in extreme temperatures or adverse weather conditions like rain or high wind speeds can cause damage and affect the quality of the slab.
- Quality of materials: Use good quality materials for the slab, including cement, sand, and aggregates, to ensure the strength and durability of the slab. The ratio of cement to mortar to sand should be as per the ratio provided by the structural engineer.
By following these precautions, you can ensure that the slab is strong, durable, and free from defects or damage.
At Smartscale we follow good practises and provide such checklist to our clients to check the same before and during the casting process.